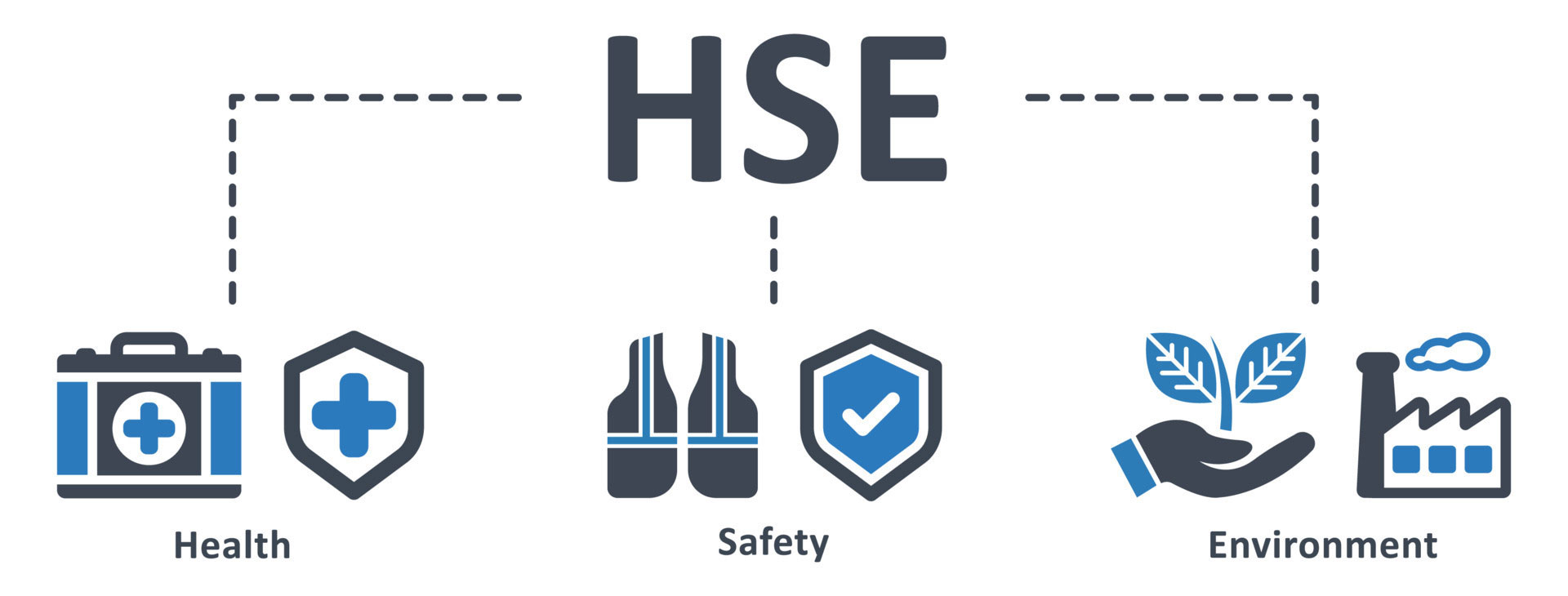
دستورالعمل سلامتی و ایمنی شیمیایی در محیط کارگاه تولید و پاشش رنگ
در این قسمت، دستورالعمل های رعایت مسائل ایمنی و بهداشتی در رابطه با پاشش رنگ صنعتی و دیگر فرآیندهای تولید مواد و پوشش های رنگی تدوین شده است.
بخش بهداشت و ایمنی شغلی
“شرکت مهندسی شیمیایی و رنگسازی نیلی فام ری“
- مقدمه
افراد شاغل در صنعت تولید رنگهای شیمیایی در حین کار، به صورت بالقوه در معرض انواع مواد خطرناک قرار دارند. این مواد شامل حلال های آلی ( تینر و رقیق کننده ها) ، رزین ها، رنگدانه ها و مواد مورد استفاده در زمان آماده سازی سطح مانند عوامل رنگ زدایی ، زنگ برها و غبارگیرها برای سمباده زنی میباشند. در معرض این مواد بودن چه به صورت استنشاق بخارات، ذرات و مواد و یا جذب از طریق پوست میتواند سبب ایجاد مشکلاتی برای سلامتی شود. از آن جا که اکثر این مواد اشتعال زا است کار نادرست و یا استفاده نامناسب از آنها میتواند سبب آتش سوزی و یا انفجار شود. ریسکهای مرتبط با استفاده و جابجایی این مواد در صنعت رنگ معمولا” بالا است مگر این که اقدامات ایمنی مناسب انجام شود.
با در نظر داشتن مدیریت ایمنی در ذهن باید یک ماشین اطمینان از ایمنی شیمیایی در محل کار یعنی یک برنامه ایمنی شیمیایی داشت و آن را اجرا و همراه با دیگر ارکان سیستم مدیریت ایمنی سازمان اجرا نمود. برنامه ایمنی شیمیایی شامل اجزایی مانند برنامه اعلام خطر، ارزیابی ریسک فرآیندها و مواد شیمیایی و اقدامات پیشگیرانه مناسب، برنامه PPE و وسایل محافظت فردی و آموزش است. جزئیات برنامه ایمنی شیمیایی در این دستورالعمل درج شده است.
این دستورالعمل برای آن است که کارکنان، پرسنل مدیریت، متخصصان، پرسنل ایمنی، ناظرین و کارکنان درگیر در صنعت رنگ و فرآیندهای پوشش رنگی مربوطه با اطلاعات تفصیلی در مورد توسعه برنامه سیستماتیک برای ایمنی شیمیایی در رنگ و فعالیت های مربوطه از آن استفاده کنند. از آنجا که هر کارگاه دارای موارد منحصر به فرد خاص خود است، کارکنان باید از این کتابچه برای توسعه برنامه ایمنی شیمیایی خاص خود استفاده کنند که این برنامه بیشترین همخوانی را با شرایط محل کار داشته و باید آموزش و تجربه کارکنان را هم در نظر داشت.
خوانندگان باید به الزامات ذیل شرایط و قوانین مربوط به بخش نامه بهداشت و ایمنی شغلی و بخش نامه تعهدات صنعتی و کارخانه ها و به ویژه باید به الزامات تعهدات صنعتی و کارخانه ها و مقررات آن توجه داشته باشد.
- خطرات پاشش رنگ و فرآیندهای تولید پوشش های رنگی مربوطه
- فرآیند پاشش رنگ
2-1-1- منظور از پاشش رنگ فرآیندی است که در آن رنگ به صورت پودر یا ذرات معلق در می آید و روی سطحی که باید پوشش دار شود قرار میگیرد تا لایه یکنواختی ایجاد شود.
2-1-2- رنگها بیشتر از حلالها (یا تینر و رقیق کنندهها)، رزین و رنگدانهها تشکیل شده اند. دیگر افزودنیها شامل سختکنندهها، خشککنندهها، ضخیمکنندهها، دیسپرس کنندهها و کشندههای سطحی هستند. اغلب حلالهای مورد استفاده در رنگها به جز آب، ترکیبات آلی بسیار فرار میباشند.
2-1-3- فرآیندهای پوششکاری مربوطه در این دستورالعمل منظور فرآیندهایی است که در آن رنگها با جلا، لاک یا دیگر سطوح جایگزین میشود. اصطلاح پاشش رنگ در این دستورالعمل شامل فرآیندهای پوششکاری هم میشود، مگر این که غیر از این گفته شده باشد.
2-1-4- پاشش رنگ معمولا” با یکی از روشهای زیر انجام میشود:
آ. اسپری بدون هوا – در این روش مایع رنگ با فشار از طریق یک اریفیس کوچک و با فشار زیاد پاشیده می شود . فشار هیدرولیک معمولاً به وسیله پمپ های پیستونی کوچک ایجاد می شود که توسط هوای فشرده پودر می شوند . در صورت افت سریع سرعت قطرات رنگ بعد از ترک نازل افزایش اسپری و کمانه ممکن است به 20 درصد برسد . این روش بیشتر برای ایجاد پوشش های قوی توپر ویسکوز استفاده می شود.
ب. اسپری تحت فشار هوا – این روش از رایج ترین روشها است که در آن رنگ مایع در نازل های میکس داخلی و بیرونی پودر یا اتمیزه میشود و این کار به کمک هوای تحت فشار پایین انجام میشود. در نازلهای میکس داخلی، هوای فشرده و مایع در محفظهای داخل نازل ترکیب میشوند در حالی که در نازلهای میکس بیرونی مایع و هوای فشرده از طریق اریفیس های مجزا تزریق میشوند تا در بیرون نازل ترکیب شود. در این روش، هدررفت رنگ مایع بیش از 50 درصد است زیرا معمولا” بخشی از مایع به سطح نمیرسد و یا از روی آن بر میگردد.
پ. روش الکترواستاتیک – قطرات مایع یا ذرات جامد دارای بار الکتریکی هستند و همین سبب میشود که به قطعه کار رسانای ذاتی بچسبند. این بار قبل از آزاد شدن به جریان مایع میچسبد و یا با عبور قطرات اتمیزه از داخل میدان یونیزه کننده وارد جریان میشود. با این فرآیند تا حد 90% پوشش را می توان روی سطح داشت.
ت. ترکیبی از فرآیندهای فوق الذکر
2-2- خطرات آتشسوزی و انفجار
2-2-1- استفاده از مواد اشتعال زا در اسپری رنگ سبب ایجاد خطرات آتشسوزی و انفجار میشود. در اسپری رنگ، قطرات رنگ پخش میشود و به سرعت فضای هوا را پر میکند و وقتی با منبع جرقه بالقوه تماس پیدا میکند مثلاً با برق ساکن، جرقه یا شعله، مشتعل میشود و ممکن است انفجار رخ دهد.
2-2-2- در فرآیند اسپری کردن تمام مایع اسپری شده روی قطعه کار نمینشیند. بخشی از آن ممکن است روی دیگر سطوح مانند دیوارهها، کفها و لباسهای افراد قرار گیرد و رسوبات اشتعالپذیر برجای بگذارد. این رسوبات میتوانند در صورت ایجاد جرقه سبب آتشسوزیهای جدی شوند.
2-2-3- آزاد شدن بخارات قابل اشتعال در فرآیند خشک شدن نیز خطرات جدی برای انفجار و آتشسوزی ایجاد میکند. بعضی از پوششها مانند لاکها حاوی 80% حلالهای فرار هستند که در زمان خشک شدن میتواند تبخیر شود.
2-3- خطرات بهداشتی
2-3-1- مواد شیمیایی خطرناک برای سلامت از سه راه اصلی وارد بدن میشوند:
آ) هضم و دستگاه گوارش
- استنشاق
پ) جذب پوست
2-3-2- اسپری رنگ مخاطرات بهداشتی زیادی دارد که اکثرا” ناشی از اجزای مخاطره دار رنگ مانند حلالها، رزینها و رنگدانهها هستند. شماری از رنگدانهها مانند رنگدانههای زرد و قرمز کرمی و استرهای حاوی سرب و دیگر فلزات سنگین ممکن است دارای اثرات بهداشتی سوء باشند. همچنین آمادهسازی سطحی قبلی مانند تمیز کردن، روغن زدایی، برداشتن رنگ یا برداشتن زنگ میتواند لازم باشد. این کار باید شامل استفاده از حلالهای سمی، مواد شیمیایی خورنده و در صورت انجام سمباده کاری ایجاد غبارات مضر باشد.
2-3-3- در صورتی که کارگران در معرض مواد خطرناک اسپری رنگ قرار گیرند اثرات بهداشتی حادی دارد.
2-3-4- اثرات بهداشتی حاد بلند مدت شامل موارد زیر است:
آ) بیماریهای حاد مجرای تنفسی
- التهابات پوستی حاد
پ) سرطان ریه
- سندرم مغزی که ناشی از این است که به صورت بلند مدت در معرض حلالهای آلی باشیم که روی مغز تأثیر دارد و
- آسیب به سیستم تولید مثل، کلیه، کبد و سیستم گردش خون
2-3-5- اثرات سلامتی کوتاه مدت شامل:
- التهابات پوستی در اثر تماس
- سوختگی چشم و پوست
- استفراغ و اسهال
- حساسیت در ناحیه بینی، گلو و ریهها
- سردرد، خواب آلودگی، تهوع و خستگی
- تنگی نفس
- برنامه ایمنی شیمیایی
- مقدمه
- برای اطمینان از ایمنی و سلامت و بهداشت کار کارکنان شاغلی که با مواد رنگی خطرناک و فرآیندهای تولید و اسپری رنگ کار دارند باید برنامههای ایمنی شیمیایی دقیق برنامه ریزی شده داشت. در این برنامه، خطرات مواد و فرآیندهای مورد استفاده در محل کار باید معلوم و به تمامی کارکنان اعلام گردد. ریسکهای ناشی از خطرات باید ارزیابی و کنترلهای لازم با توجه به کارایی اقدامات باید انجام شود. برنامه ایمنی شیمیایی شامل دیگر اجزا مانند وسایل حفاظت فردی، برنامه ریزی و آموزش اضطراری برای کارکنان نیز میباشد.
- جوانب فوق در مورد برنامه ایمنی شیمیایی باید به خوبی سازماندهی و در سیستم مدیریت ایمنی نیروی کار وارد شود. به عبارت دیگر، شرکت باید دارای خط مشی ایمنی خاص خود، پرسنل مسئول و منابع و امکانات مورد نیاز برای توسعه، پیاده سازی و نگهداری برنامه ایمنی شیمیایی باشد.
- اجزای اصلی
- اجزای اصلی برنامه ایمنی شیمیایی در فرآیندهای تولید و پاشش رنگ باید شامل بخشهای زیر باشد:
آ) اعلام خطر- برای تعیین وسایل و ابزارهای مناسب جهت ارسال اطلاعات ایمنی و بهداشتی در مورد مواد شیمیایی و فرآیندهای تولید و پاشش رنگ به کارکنان
- ارزیابی ریسک – برای ارزیابی ریسک در تعهدات
پ) اقدامات ایمنی- برای استفاده و ادامه اقدامات پیشگیرانه و کنترلی
- اعلام خطر
- مقدمه
- بر اساس شرایط و مفاد بخش نامه ایمنی و بهداشت شغلی، کارکنان متعهد به ارائه این اطلاعات در صورت نیاز و برای اطمینان از ایمنی و بهداشت کارکنان خود در کار هستند. برنامه اعلام خطر برای انتقال این اطلاعات در مورد مواد و فرآیندهای مورد نظر به کارکنان است.
- کارکنان باید ابتدا تمامی مواد شیمیایی خطرناک مورد استفاده یا آزاد شده در فرآیندهای تولید و پاشش رنگ در محل کار خود را شناخته و لیست کنند. این لیست باید جامع و با توجه به برگههای ایمنی مواد یا MSDS یا اطلاعات معادل به دست آمده از تولیدکنندههای محصولات شیمیایی و منابع دیگر چک شوند و همچنین آنها باید اطمینان یابند که این اطلاعات در مورد مواد شیمیایی، برچسب ها و رویههای فعالیت استاندارد به خوبی از طریق برنامههای آموزشی صحیح و یا ابزارهای دیگر به کارکنان منتقل میشود.
- مقدمه
- منابع اطلاعات خطرناک
2-2-1- اطلاعات مخاطرات مهم و اصلی روی برچسب ظرفهای مواد بسیار محدود است اما ضرورت دارند درحالی که از MSDSمربوطه ارائه شده توسط تولید کنندههای مواد شیمیایی (سازندههای مواد، وارد کنندهها و پخش کنندهها) میتوان اطلاعات بیشتری به دست آورد. دیگر منابع اطلاعاتی باید شامل کاتالوگهای شیمیایی، مجلات شیمی، هندبوکهای شیمی و پایگاه دادههای آنلاین باشند.
2-2-2- کیفیت برنامه اعلام خطر به کفایت و دقت ارزیابی ریسک در کارگاه بستگی دارد. بنابراین کارکنان باید تلاش کنند تا اطلاعات کافی و بروز را در مورد مواد خطرناک از تأمین کننده موقع ارزیابی ریسکهای مواد به دست آورند.
2-3- ابزارهای اعلام خطر
2-3-1- کارفرماها باید اطمینان یابند که کارکنان خطرات مواد شیمیایی در تولید و اسپری رنگ را میشناسند و درک میکنند. ابزارهای اعلام خطر شامل برچسبها، MSDS، رویههای فعالیت استاندارد و آموزش آنها است. کارفرماها میتوانند از پلاکاردها، اعلامیه و تابلوهایی مفید برای محل کار خود نیز استفاده نمایند.
برچسبها:
2-3-2- برچسب زدن روی ظرف حاوی مواد خطرناک از جمله روشهای مستقیم ارائه اطلاعات خطر است. این برچسب باید شامل اطلاعات خطر زیر باشد:
آ) شناسایی مواد – نام شیمیایی و نام رایج
- دسته بندی خطر و علائم خطر
پ) ریسکهای خاص ذاتی مواد و
- اقدامات احتیاطی ایمنی مورد نیاز
2-3-3- اگر از نظر عملی امکان برچسب زدن به ظرف حوای مواد خطرناک نباشد، اعلام اطلاعات مربوطه باید به شکل زیر باشد:
آ) به زبان فارسی و انگلیسی
ب) شناسایی و معلوم نمودن ظرف یا ظروف حاوی مواد
پ) تعیین ویژگیهای مورد نیاز و الزامی بر اساس تعهدات صنعتی و کارخانهها در قوانین مربوط به مواد خطرناک
- در محلی مشخص و شناخته شده نزدیک مواد خطرناک و
- با علائم و علامتهای مورد نیاز که باید در فضایی تا یک دهم محل اطلاعیه نمایش داده شود.
الزامات تفصیلی در مورد برچسب زدن مواد خطرناک در قوانین مواد خطرناک تعهدات صنعتی و کارخانهها آمده است.
برگههای دادههای ایمنی مواد یا : MSDS
2-3-4- MSDSحاوی اطلاعات تفصیلی خطر است و فرمت استاندارد آن بر اساس استاندارد 11014-1 ISO باید حاوی اطلاعات زیر باشد که بخش اعظم آن برای ارزیابی ریسک ضروری است:
- شناسایی محصول و شرکت
- ترکیب و اطلاعات مربوط به اجزای تشکیل دهنده
- شناسایی خطرات
- اقدامات کمکهای اولیه
- اقدامات آتشنشانی
- اقدامات آزاد شدن اتفاقی مواد
- جابجایی و انبار
- کنترل در معرض بودن و یا حفاظت فردی
- خواص شیمیایی و فیزیکی
- ثبات و واکنش دادن
- اطلاعات سم شناسی
- اطلاعات اکولوژیکی
- ملاحظات امحا
- اطلاعات انتقال
- اطلاعات نظارتی و
- اطلاعات دیگر
2-3-5- نسخهای از MSDSهر ماده خطرناک باید در محل کار نگهداری شود و باید به راحتی در اختیار کارکنان قرار گیرد. این برگههای دادههای ایمنی در ارزیابی ریسک خطرات مربوط به استفاده و جابجایی مواد ارزشمند است.
رویههای فعالیت استاندارد:
2-3-6- اطلاعات خطرات در مورد تولید و اسپری رنگ باید به وضوح در رویههای فعالیت استانداردی که کارکنان باید از آنها تبعیت نمایند درج شود.
آموزش (بخش 8.3 را ملاحظه کنید):
آموزش نحوه اجرای برنامههای اعلام خطر باید ارائه شود. کارکنان نیز باید اطمینان یابند که نحوه دسترسی به اطلاعات خطر را میدانند و اطلاعات روی برچسبها و MSDSمواد شیمیایی را درک میکنند.
3- ارزیابی ریسک
- مرور کلی
3-1-1- ارزیابی ریسک فرآیندی برای ارزیابی خطراتی است که مواد شیمیایی و فرآیندها ممکن است در کار به بار بیاورند و شدت و احتمال آنها مشخص شود و نیز باید اقدامات کنترلی مناسب برای کاهش خطرات انجام شود.
3-1-2- دستورالعمل ایمنی شیمیایی در محل کار: دستورالعمل ارزیابی ریسک و اصول اقدامات ایمنی صادره توسط وزارت کار اصول و روشهای سیستماتیکی را برای اجرای ارزیابی ریسک در رابطه با خطرات مواد شیمیایی دارد.
3-1-3- ارزیابی ریسک باید توسط افراد ذیصلاح با تجربه مناسب و آموزش در فعالیتهای کاری تولید و پاشش رنگ انجام شود. این افراد باید دارای شناخت مناسب از مواد شیمیایی و فرایندهای رنگ پاشی باشند که ارزیابی می شوند و نیز باید اطلاعات خوبی در مورد اقدامات ایمن مورد نیاز موجود باشد . همچنین باید با متخصصان برای اخذ نظریات تخصصی مشورت شود .
3-2- ارزیابی ریسک
3-2-1- کارکنان باید اطمینان یابند که یک ارزیابی ریسک باید در تمامی کارهای تولید و پاشش رنگ مربوط به در معرض مواد بودن و فرآیندها انجام شود.
3-2-2- موقع در نظر گرفتن تأثیرات بالقوه بهداشتی، باید در معرض مواد خطرناک هوازی بودن کمتر از حدود در معرض بودن شغلی یا OEL مندرج در آیین نامه رفتاری کنترل ناخالصیهای هوا یا مواد شیمیایی در محل کار صادره توسط وزارت کار باشد. مقادیر OELS غلظتهای هوازی مواد شیمیایی است که در کمتر از آن اثرات بهداشتی حاد تقریبا” تمامی کارکنان وجود ندارد اگر به صورت استنشاقی در معرض آن باشند. برای این موارد نیازمند پایش و کنترل هوا هستیم.
3-2-3- از آنجا که OELسطح بی اثری را نشان نمیدهد که در آن هر کارمندی کاملا” محافظت شود، بلکه کارفرماها نیز باید موارد زیر را مورد توجه قرار دهند:
آ) چگونه مطمئن شوند که استانداردهای در معرض قرار گرفتن تحت هیچ شرایطی نقض نمیشوند.
ب) سطح در معرض بودن تا حد منطقی و عملی پایین باشد.
پ) میزان در معرض بودن در آینده و هر موقع که از نظر عملی ممکن بود صفر یا کم شود.
3-2-4- راه عملی برای اجرای ارزیابی ریسک در فرآیندهای تولید و پاشش رنگ شامل مراحل زیر است:
مرحله اول:
3-2-5- مرحله اول فهرست نمودن تمامی مواد مورد استفاده یا تولید شده در فرآیند تولید و پاشش رنگ مثلا” در رنگها، حلالها، رزینها، پودرها و مواد آماده سازی سطحی مانند چسبها، رنگ برها، تبدیل کنندههای زنگ و غبارهای ناشی از سمباده است.
مرحله دوم:
3-2-6- مرحله دوم به دست آوردن و بررسی اطلاعات مربوط به خطرات آنها از روی برچسبهای ظرف و دیگر برگههای MSDSاست.
3-2-7- مواد خطرناک را میتوان در سه دسته خطر زیر دسته بندی نمود یعنی خطر بالا، متوسط و پایین به شرح زیر:
آ) خطر بالا: شامل موادی با اجزای زیر هستند:
- مواد ایجاد کننده سرطان مثلا” قطران زغال سنگ،
- حساس کنندههای تنفسی یا پوستی مثلا” ایزوسیاناتها در رنگهای پلی یورتان
- خطرات تکثیری و موتاژن ها مثلاً اتوکسیتیل استات
- موادی که سبب ایجاد اثرات شدید بعد از تکرار یا در معرض طولانی بودن میشوند مثل استیرین
- مواد خطرناک فلزی مانند کادمیم
- موادی که سبب اثرات غیر قابل برگشت کشنده و غیره کشنده بعد از یکبار در معرض قرار گرفتن میشوند.
- موادی که سبب ایجاد اثرات حاد و حساسیت زا میشوند.
- موادی که در زمره مواد سمی قرار میگیرند.
- موادی که در ردیف مواد خورنده قرار دارند.
- موادی که سبب احتراق می شوند.
- دو یا چند جزئی بودن رنگ مانند رنگ پولی یورتان و سخت کننده آن
- خطرات متوسط: شامل هر نوع مادهای که حاوی حلالهای آلی است یا مایعی قابل اشتعال است که در دسته بندی خطرات بالا قرار نمیگیرد.
پ) خطرات پایین: شامل هر ماده دیگری است که در بالا به آن اشاره نشده است.
مرحله سوم:
3-2-8- مرحله سوم بررسی و بازرسی محل کار و رویههای برای یافتن افرادی است که در معرض مواد خطرناک هستند که شامل موارد زیر است:
آ) بحث با کارکنان در مورد اقدامات کاری آنها و رویهها و محیط
- تعیین این که آیا مواد خطرناک در محیط کار رها میشوند و توجه خاص به 1- علائم آلودگی و 2- تجربه افراد و یا علائم در معرض بودن
پ) توجه به دیگر افراد بالقوه در معرض شامل افراد عبوری، کارکنان بخش نگهداری و نظافت
ت) توجه به اثرات شرایط خاص و غیر عادی
ث) توجه به اثرات ترکیبی دو یا چند ماده خطرناک
ج) برآورد میزان در معرض بودن مثلا” میزان، فراوانی، مدت در معرض بودن و مسیرهای مختلف ورود و خروج
چ) توجه به اقدامات کنترلی فعلی برای یافتن این موارد:
- کنترلهای مناسب قبلا” در محل انجام و به صورت مؤثر ادامه یابد.
کارکنان در استفاده از این کنترل کنندهها آموزش دیده باشند.
مرحله چهارم:
3-2-9- مرحله چهارم درجهبندی ریسکهای مربوط به مواد و فرآیندهای خطرناک تولید و پاشش رنگ یعنی مشخص نمودن میزان بزرگی ریسکها است. درجهبندی ریسکها به احتمال برآورد شده و شدت بالقوه خطرات بستگی دارد. از طرفی، شدت خطرات و یا آسیبهای آن به عوامل مختلفی مانند دستهبندی خطر آن (بالا، متوسط و یا پایین) و میزان مواد شیمیایی مورد استفاده بستگی دارد. معمولا” درجهبندی ریسکها را میتوان به شرح جدول زیر خلاصه نمود:
– | اندکی مضر | مضر | شدیدا” مضر |
به شدت غیر محتمل | ریسک پایین | ریسک متوسط تا پایین | ریسک متوسط |
غیرمحتمل | ریسک متوسط | ریسک متوسط تا بالا | ریسک بالا |
محتمل | ریسک متوسط تا بالا | ریسک بالا | ریسک بالا |
3-2-10- ریسکهای مرتبط با مواد و فرآیندهای خطرناک را میتوان به شرح زیر در سه دسته بالا، متوسط و یا پایین دستهبندی نمود:
آ) ریسک بالا است- ضربات و صدمات بالقوه جدی است و احتمال در معرض قرار گرفتن بالا است. مثلا” مواد یا فرآیندها خطرات بالایی دارند و غبارها و رطوبت و بخارات در هوا دیده میشوند و شکایت از بیماریها و ناراحتیها و حساسیتها زیاد است و این در حالیست که کارکنان آموزش ندیدهاند.
- ریسک متوسط است- مواد یا فرآیندها خطر متوسط دارند و چندین کارمند وجود دارند که میتوانند به صورت روزانه در معرض آن قرار گیرند و استفاده از این ماده بر اساس MSDS و از طریق کنترلهای مؤثر مهندسی قویا” کنترل میشود.
پ) ریسک کم است و محتمل نیست افزایش یابد:
- به سختی خطری وجود دارد مثلا” به خاطر این که میزان ماده مورد استفاده خیلی کم است که منجر به آسیب شدیدی شود حتی اگر کنترلها انجام نشود.
- مواد یا فرآیندها میتوانند سبب اثرات کم شوند اما استفاده از آن بر اساس MSDSیا الزامات بهداشتی مناسب قویا” کنترل میشود و کارکنان آموزش دیدهاند.
3-2-11- بعد از تکمیل مراحل ارزیابی فوق، تصمیماتی در رابطه با موارد زیر اتخاذ میشود:
آ) برنامهریزی و ایجاد و استفاده از اقدامات کنترلی مناسب برای برآورده نمودن نیازهای مندرج 1- قوانین بومی و آیین نامههای رفتاری مربوطه 2- کتابچههای راهنمای صادره توسط اداره کار یا دیگر سازمانهای مرتبط و 3- بهترین اقدام و عملکرد تجاری
- اطمینان از اجرای درست و ادامه اقدامات کنترلی مناسب
پ) آموزش کارکنان
- تصمیمگیری در مورد این که آیا پایش و مراقبت بهداشتی مورد نیاز است یا خیر
- ارائه رویههای اضطراری و اورژانسی و کمکهای اولیه مناسب و
- مرور و توسعه رویههای کاری استاندارد در صورت لزوم
3-2-12- اگر ریسک بالا باشد، اقدامات کنترلی لازم باید مشخص، اتخاذ و قبل از استفاده از مواد شیمیایی و یا اجرای رویههای خطرناک پیاده شوند. پایش و مراقب بهداشتی باید برای ارزیابی کارایی این اقدامات اجرا شوند. شرط و نیاز به کنترل بلند مدت باید مشخص و انجام گیرد.
3-2-13- اگر ریسک متوسط باشد، اقدامات ایمنی جبرانی باید در زمان مناسب انجام شود.
3-2-14- تنها وقتی ریسک پایین است، میتوان آن را با بهبود بهتر و تشخیص مناسب قابل تحمل دانست.
3-3- ثبت دادهها
3-3-1- کارکنان باید یافتههای ارزیابی را ثبت نمایند و این موارد ثبتی به ردیابی منطق نتایج قبلی کمک میکند و اطلاعات مهمی برای مرور و بازبینی آینده ارزیابی دارد.
3-4- مرور ارزیابیها و بازبینی آن
3-4-1- ارزیابی ریسک باید به صورت منظم باشد و هر موقع مدرکی، دیگر معتبر نباشد و یا در آن تغییرات زیادی رخ دهد باید مجددا” ارزیابی شود.
3-4-2- اطلاعات زیر باید حاوی نکاتی باشد که نشان دهد که ارزیابی ریسک دیگر اعتبار ندارد:
آ) نتایج کنترل عملکرد منظم تجهیزات
ب) نتایج پایش و کنترل آلودگی جوی اجرا شده در محیط کارها
پ) وقوع رخداد یا سانحهای مهم
- نتایج مراقبت بهداشتی
- اطلاعات جدید در مورد خطرات بهداشتی مربوطه
3-4-3- تغییرات مهم در فرآیندهای پاشش رنگ شامل موارد زیر است:
آ) تغییرات در مواد خطرناک مورد استفاده که شامل اشکال فیزیکی و منبع مواد است.
- اصلاح و تغییرات در دستگاهها شامل تجهیزات مورد استفاده در اقدامات کنترلی
پ) تغییرات در روش و رویههای کاری
ت) تغییرات در مقیاس و بزرگی فرآیند
- اقدامات ایمنی
- استراتژی کلی
- در انتخاب اقدامات ایمنی مناسب، باید در اصل به ترتیب اولویت به موارد زیر توجه نمود:
- استراتژی کلی
آ) دفع خطرات
- جایگزینی با روشهای کم خطرتر
پ) جداسازی و تفکیک فرآیندهای پاشش رنگ
- کنترلهای مهندسی
- کنترلهای اجرایی
- استفاده از وسایل حفاظت فردی یا PPE
- دفع کامل خطرات باید انتخاب اول باشد. اگر در عمل ممکن نباشد، اقدام دوم در سلسله مراتب است و جایگزینی را باید در نظر گرفت. استفاده از PPE باید تنها وقتی در نظر گرفته شود که سطوح بالاتر اقدامات ایمنی عملی و یا ناکافی باشد.
- در بعضی از موارد، بهتر است از ترکیب دو یا چند اقدام ایمنی استفاده نمود تا اطمینان یابیم که ریسکها دفع شده و یا تا پایینترین سطح کم شدهاند.
- کارکنان باید تلاش کنند تا اقدامات ایمنی را در بخش بالای سلسله مراتب به صورت بلند مدت انجام دهند. به عنوان مثال، دفع و یا جایگزینی مواد خطرناک شاید اکنون و در حال حاضر عملی نباشد بلکه در آینده و با پیشرفت علم و فنآوری قابل اجرا هستند.
- دفع و حذف
4-2-1- این مؤثرترین اقدام ایمنی است که با متوقف نمودن استفاده از مواد و یا دستگاههای دارای ریسک متوسط و یا بالاتر حاصل میشود.
- جایگزینی
4-3-1- منظور از جایگزینی استفاده از مواد کم خطرتر، دستگاههای کم خطر و یا فرآیندهای کم خطر برای انجام یک کار است.
4-3-2- اقدامات جایگزینی شامل موارد زیر است:
آ) جایگزینی مواد و رویههای خطرناک با مواد کم خطرتر. به عنوان مثال، رنگ های مایع اشتعال پذیر را با رنگهای پایه آب یا کم اشتعال جایگزین نمایید و یا فرآیندهای پاشش رنگ را غلتک، برس و یا مغروق سازی جایگزین نمایید.
- آیتم خطرناک دستگاه ها را با آیتمهای کم خطرتر تعویض کنید.
- جدا سازی
- جداسازی به معنای تفکیک کارکنان از خطرات به وسیله موانع فیزیکی، فاصله دادن و یا زمان دادن است. این کار میتواند با اتوماسیون و یا تفکیک انجام شود.
- جدا سازی
اتوماسیون فرآیند
- فرآیندهای تولید و پاشش رنگ باید کاملا” بسته باشند اگر کاملا” اتوماتیک باشد، این شکل بسیار مؤثری از جداسازی است زیرا این فرآیند کاملا” محصور است و هرکسی میتواند از خطرات جدا و تفکیک شود.
جداسازی فرآیند
- فرآیندهای اسپری نمودن با استفاده از مایعات اشتعال پذیر میتواند در اتاقک اسپری ساخته شده از مصالح نسوز انجام شود. مصالح نسوز نیازمند دوره مقاومت به آتش 1 ساعت برای کفها، دیوارها و سقف و نیم ساعت برای پنجرهها و دربها است.
- اگر تهیه اتاق اسپری مجزا ممکن نیست، فرآیند اسپری نمودن باید در محل اسپری مشخص شده انجام شود و در این بخش اسپری نمودن باید در داخل یک اتاقک بسته انجام شود. بازشوهای با اندازه مناسب در اتاقک یا کابینت برای کار و تهویه در نظر گرفته شده است.
- اتاقک اسپری و یا محل خاص آن شامل اتاقکها و یا غرفههایی است که باید تهویه شود و به فضای باز راه داشته باشد و بدین منظور باید از وسایل مکانیکی مناسب برای دفع مواد و بخارات اشتعال پذیر و خطرناک ناشی از فرآیند اسپری استفاده شود.
- کنترلهای مهندسی
- کنترلهای مهندسی مستلزم استفاده از اصول مهندسی و اقدامات برای کاهش ریسک است. کنترلهای مهندسی برای اسپری رنگ شامل موارد زیر است:
آ) تهویه
- ایمنی الکتریکی
پ) محل و طراحی شیلنگ های فشار قوی و لوله ها
- کنترلهای مهندسی میتواند ایجاد مواد خطرناک در زمان اسپری نمودن را حداقل و یا خاموش و یا محصور نماید و محل آلودگی را در صورت نشتی محدود نماید.
تهویه
- تهویه به کاهش خطرات ناشی از بخارات و ذرات ایجاد شده در زمان تولید و پاشش رنگ کمک میکند و مانع استنشاق مواد خطرناک میشود. همچنین ابزاری مهم برای کاهش تماس چشم یا پوست با مواد خطرناک میشود و برای کنترل خطرات آتشسوزی و انفجار اهمیت دارد. در این بین تهویه اسپری زیاد را از اپراتور دور و قبل از تخلیه آن را شسته و یا فیلتر میکند.
- انواع تهویه برای کارگاه تولید و اسپری رنگ عبارتاند از:
آ) اتاقک پاشش
- تهویه تخلیه موضعی
پ) تهویه رقیق سازی
تهویه – اتاقکهای پاشش
- اتاقک پاشش شکل بسیار مؤثر تهویه برای پاشش رنگ است. بنابراین پاشش رنگ باید حتیالامکان همیشه در اتاقک پاشش انجام شود.
- دو نوع اتاقک پاشش عبارتاند از:
آ) اتاقک با جریان جانبی- جریان هوای داخلی نوع افقی است که میتواند در پاشش ذرات متوسط و کوچک و موارد قابل چرخش استفاده شود. میزان بسته بودن و انحصار میتواند تغییر نماید اما هرچه محصوریت بیشتر باشد راحتتر میتوان پخش رنگ را کنترل نمود.
- اتاقک با جریان زیرین- با تهویه رو به پایین، این اتاقک در اسپری ذرات بزرگ استفاده میشود که در آن دسترسی همه جانبه لازم است و استفاده از یک ماده قابل چرخش ممکن نیست. این اتاقک امکان حرکت آزادانه دور ماده را فراهم مینماید و اپراتور هرگز در پایین دست ذرات نیست. هوا از طریق سقف باز و یا سیستم تعویض هوا وارد اتاقک میشود و از طریق کف نیز وارد میشود و هدف آن شستن محفظهها در امتداد کنارههای اتاقک است.
- اتاقک اسپری باید بر اساس استانداردهای داخلی و جهانی طراحی، ساخته، نصب و نگهداری شود. اتاقک اسپری شامل سیستم تهویه خروجی است و بنابراین جریان پیوسته و یکنواخت هوا را در سراسر محل اسپری تا خروجی فراهم مینماید.
- کارگر مسئول اسپری هرگز نباید موقع کار در اتاقکهای اسپری بین تفنگ اسپری و خروجی هوا باشد.
- هوای تازه باید از منبع غیر آلوده کشیده شود و هوای آلوده باید به سمت محل تخلیه شود که خطر و یا آلودگی برای محل کار نداشته باشد.
تهویه – تهویه خروجی موضعی
- سیستمهای تهویه خروجی موضعی معمولا” برای کنترل آلودگی در زمان انجام فعالیتهای تولید و اسپری رنگ استفاده میشود و در آن بخارات حلال و اضافی تا حد امکان به منبع آزادسازی نزدیک میشود. این سیستمها باید دارای فیلترهای ذرات برای فیلتر نمودن اسپری اضافی باشند.
- تهویه خروجی موضعی ماده اضافی اسپری و بخارات حلال را با کشیدن آلایندهها به داخل هود میگیرد. از آنجا که هود طرحهای مختلفی دارد، کارفرماها باید هودهای مناسب و مؤثری را برای فرآیندهای کاری انتخاب کنند.
- تهویه خروجی موضعی باید برای اسپری رنگ داخلی موقع عدم استفاده از اتاقک در دستور کار باشد. از این گذشته، میتوان از تهویه همراه با دیگر اقدامات کنترلی مانند ایزولاسیون برای اسپری رنگ بیرونی استفاده نمود.
تهویه- تهویه رقیق
- تهویه رقیق شامل رقیقسازی و جابجایی هوای آلوده با هوای تازه است. هوای تازه به وسیله فنهای ورودی مکانیکی یا جریانات هوای طبیعی از دربها، پنجرهها و یا بازشوهای دیگر در محل کار وارد محل کار میشود. هوای آلوده با فشار از بازشوهای کمکی بیرون فرستاده میشود و یا با فن تخلیه، تخلیه میگردد.
- این روش تنها برای تأمین هوای ثابت مناسب است و باید همراه با دیگر روشهای مؤثر تهویه استفاده شود تا آلودگیهای هوازی ساطع شده از فرآیند اسپری رنگ را بردارد. تهویه رقیقسازی میتواند تهویه خروجی موضعی مکمل برای کنترل ریسکهای برگشت مواد خطرناک و آتشسوزی بخارات اسپری رنگ و ذرات در موقع عدم امکان استفاده از اتاقک به حساب آید.
- سیستم تهویه رقیقسازی باید به گونهای طراحی، ساخته، نصب و اجرا شود که کارایی آن حداکثر گردد.
ایمنی برقی
- اسپری رنگ بی هوا با استفاده از فشار بالای سیال میتواند الکتریسیته ساکنی ایجاد کند که سبب جرقه شود. بنابراین تفنگ اسپری بدون هوا و دیگر اقلام رسانای مورد استفاده در اسپری مانند ظرف و تفنگ اسپری باید دارای اتصال بدنه یا سیم ارت برقی باشند.
- کارفرماها باید مطمئن شوند که شیلنگها و لولهها به گونهای قرار گرفته اند که:
آ) امکان نشتی و گسیختگی آنها وجود ندارد و
ب) در صورت نشتی و پارگی، مواد قابل اشتعال وارد محیطی که منبع جرقه است نشود.
- کنترلهای اداری و اجرایی
4-6-1- کنترلهای اداری و اجرایی شیوههایی برای سازماندهی کارها هستند تا کار، ایمن شود که نمونه آن کاهش در معرض بودن افراد و یا کاهش تماس با موادخطرناک و یا فرآیندهای تولید و اسپری از طریق سازوکارهای اجرایی مانند شیفتهای چرخشی، مرخصی و غیره است و جزئیات اقدامات ایمنی کاری در فصل 7 شرح داده شده است.
- تجهیزات و وسایل برقی
- تجهیزات برقی در یک کارگاه تولید و اسپری رنگ شامل فنها، میزگردها، چراغهای خشک سازی، کلید و سیستم روشنایی، وسایل گرمایشی، دستگاههای مورد استفاده برای تمیز کاری و تعمیر و وسایل مورد استفاده برای میکس نمودن فرمولهای رنگی میباشد.
- تمامی وسایل و دستگاههای برقی به صورت بالقوه در معرض فضای قابل اشتعال ناشی از فرآیندهای تولید و اسپری رنگ هستند. بنابراین این تجهیزات باید به گونهای طراحی، ساخت و نصب و نگهداری شوندکه مانع جرقه فضای قابل اشتعال گردند .
- تمامی وسایل برقی مانند ابزارهای برقی دستی باید دارای محافظ نشت جریان برق ارت با ابزارهای جریان پسماند باشند.
- تجهیزات حفاظت فردی یا PPE
4-8-1- تجهیزات حفاظت فردی مانعی هستند که از کارکنان در برابر مواد شیمیایی و خطرات آن محافظت مینمایند. اما استفاده از PPE به عنوان اقدامی ایمنی باید تنها محدود به وضعیتهایی باشد که در آن تمامی اقدامات ایمنی دیگر عملی نیستند و یا در آن PPEهمراه با دیگر اقدامات برای افزایش سطح حفاظت انجام شود مثلا” برای اسپری رنگ در جایی که سرریز اسپری کاملا” حذف نمیشود و نیز استفاده از وسایل محافظتی و تنفسی برای تکمیل کنترلهای مهندسی ضرورت دارد.
4-8-2- استفاده از PPE راهی غیرعامل برای محافظت از کارکنان است. با مدیریت ایمنی هوشمندانه در توسعه برنامههای مؤثر PPE، این شیوه کار ایمنی غیرعامل میتواند به روشی فعال تبدیل شود. خوانندهها میتوانند در این موارد به ایمنی شیمیایی در محل کار: دستورالعمل وسایل حفاظت فردی برای استفاده و جابجایی مواد شیمیایی از نشریات وزارت کار مراجعه نمایند.
4-8-3- PPE باید:
آ) به خوبی انتخاب و با سایت و وظایف کار انطباق داشته باشد.
ب) تمیز، کاری و به راحتی در دسترس باشد.
پ) به خوبی انبار و در محل کار تولید و اسپری جا گذاشته نشود.
ت) درست استفاده و بر اساس دستور سازنده به صورت منظم نگهداری شود.
ث) برای فرد باشد و اسم او روی آن درج شده باشد.
- قبل از استفاده آموزشهای لازم در این زمینه ارائه شود.
4-8-4- کارکنان باید PPE خود را بر اساس آموزشها استفاده، انبار و نگهداری نمایند.
4-8-5- موقع انتخاب PPE و برنامهریزی فرآیندهای کاری نیازمند استفاده از PPE ، باید به محدودیتهای PPE و نیز کنترل ریسکهایی توجه نمود که ممکن است در اثر PPE رخ دهد مثلا” فشار و تنش گرمایی، محدودیت دید، تحرک و ارتباط با دیگران.
4-8-6- برای فرآیند تولید و اسپری رنگ، انتخاب وسایل تنفسی به موارد زیر بستگی دارد:
آ) OEL برای قطعات رنگی مختلف
- برگه داده های ایمنی سازنده و یا MSDSبرای محصولات شیمیایی
پ) تهویه محل استعمال رنگ
- میزان و مدت در معرض بودن
- عامل محافظت از ماسک
- استانداردهای ملی و جهانی مربوط به استفاده از PPE
4-8-7- به طور کلی، ماسک بخارات آلی و ذرات حداقل نیاز برای محافظت فرد در برابر پودرهای رنگی و حلالهای آلی است. اگر از ماسک نیم صورت استفاده شود، باید حفاظ چشمی و صورتی دیگری را در برداشت.
4-8-8- برای اسپری نمودن ذرات بزرگ در یک اتاقک اسپری، مثلا” اسپری رنگ روی خودروها، میزان اسپری اضافی بالا است. بنابراین ماسکهای خط هوا باید به همراه دیگر نیازهای تهویهای استفاده شوند.
4-8-9- انتخاب PPE برای اسپری رنگ در رابطه با حفاظت پوست بیشتر به مقاومت شیمیایی مورد نیاز بستگی دارد. همچنین باید به اطلاعات مربوط به خواص مقاومت شیمیایی و مشخصات فیزیکی PPE ارائه شده سازنده توجه نمود.
4-9- پایش، کنترل و مراقبتهای بهداشتی
4-9-1- پایش و کنترل ابزاری به دست میدهد تا مطمئن شویم که اقدامات ایمنی اتخاذ شده در تولید و اسپری رنگ در محافظت از کارکنان در برابر آسیبها و مریضی ناشی از خطرات مواد و فرآیندهای شیمیایی مؤثر است. در اسپری رنگ، پایش محیط کار مستلزم سنجش غلظت آلایندههای هوا در محلهای استراتژیک در محل کار یا در محل تنفس کارگران است. پایش و کنترل میتواند پیوسته و یا متناوب باشد و میتواند وسایل آشکارساز مناسب انجام شود که شامل سنسور هشدار دهنده، سنجه خواندن مستقیم، نمونهگیر استاتیکی و نمونهگیر فردی است.
4-9-2- بر اساس نتایج فعالیتهای کاری و ارزیابی ریسک، کارکنان باید یک برنامه پایشی را ایجاد و اجرا کنند و با آن کارایی کنترل آلایندههای هوازی را بر اساس حدود انفجار پایین و یا حدود در معرض شغلی کنترل مینمایند. برنامه پایش شامل موارد زیر است:
آ) پایش پارامترها
- فراوانی پایش
پ) محل و روش پایش
ت) میزان و سطح هشدار بر اساس حدود پذیرش
- اقدامات بعدی
اگر پایش نشان دهد که حدود پذیرش نقض شدهاند، فرآیند مربوطه باید معلق و علل آن بررسی شوند. سپس باید اقدامات جبرانی انجام شود که شامل بازبینی و مرور رویههای کاری استاندارد مربوطه و اقدامات ایمنی و انجام اصلاحات مناسب است. تحت هیچ شرایطی کارکنان نباید در معرض آلایندههای هوازی باشند که از حد مجاز بیشتر است.
4-9-3- در محل تولید رنگ، تمامی وقایع خطرناک و سوانح مستلزم کار با فرآیندهای شیمیایی و فرآیندهای مربوطه باید بررسی و به عنوان اقدامی برای عبرت گیری از اشتباه در نظر گرفته شود. بررسی و تحقیقات باید به ریاست مدیر خط، پرسنل ایمنی و یا فرد متخصص دارای اطلاعات در مورد این فعالیت باشد. تحقیقات باید موارد زیر را مشخص نماید:
آ) علت و یا علل وقایع و سوانح خطرناک
- علل کارایی و عملکرد پایین تر از حد استاندارد
پ) علل خطاها
محقق باید اقداماتی را نیز پیشنهاد نماید تا از وقوع و تکرار سانحه جلوگیری شود و مدیریت باید اطمینان یابد که پیشنهادات اجرا میگردند.
4-9-4- برای کارکنانی که به صورت منظم در معرض مواد شیمیایی خطرناک در محل کار هستند، مراقبتهای بهداشتی میتواند ابزاری مناسب و مؤثر برای آشکارسازی اثرات بهداشتی سوء در مراحل اولیه باشد و از صدمات بیشتر جلوگیری نماید. به علاوه نتایج مراقبت بهداشتی میتواند به موارد زیر کمک کند:
آ) کنترل کارایی اقدامات ایمنی
ب) ارائه بازخورد در مورد دقت ارزیابی ریسک
پ) مشخص نمودن و محافظت از افراد مبتلا که در معرض خطر هستند.
4-9-5- مراقبت بهداشتی شامل پایش بیولوژیکی، پیش تخصیص و معاینات پزشکی منظم، و نیز معاینات پزشکی برای معافیت از کار بعد از غیبت طولانی به دلایل بهداشتی در حین و بعد از پایان کار با مواد شیمیایی است.
4-9-6- اگر موارد یا موارد مشکوکی از مریضی به خاطر در معرض مواد شیمیایی بودن کشف شود، فعالیتها باید تعلیق و علل آن بررسی شود . سپس باید اقدامات اصلاحی انجام شود که شامل بازبینی رویههای فعالیت مربوطه، اقدامات کنترل و حفاظت و انجام اصلاحات مناسب است.
4-10- بازبینی اقدامات ایمنی
4-10-1- تمامی اقدامات ایمنی باید بازبینی شوند تا اطمینان حاصل گردد که مؤثر بودهاند و باید برای بهبود آنها اقداماتی انجام شود. در دوره بازبینی، فرصتهای رفع خطر نیز باید در ذهن باشد و مورد توجه قرار گیرد.
4-10-2- کارکنان باید مطمئن شوند که اجرا و پیادهسازی اقدامات خطرات بیشتر ایجاد نمیکند. کارکنان باید فورا” هرگونه عیب و نقصی که در اقدامات ایمنی، تجهیزات، وسایل و برچسب زنی وجود دارد را به مقامات بالاتر گزارش نمایند.
4-10-3- طرحهای بلند مدتی باید برای بهبود ایمنی و بهداشت در محل کار تدوین شود که هدف آن وارد نمودن تدریجی اقدامات بازدارنده در سیستمهای مدیریتی و اتخاذ کنترلهای با اولویت بالاتر است.
- اقدامات کاری ایمنی
- بازبینی و کنترل
- کارفرماها باید اقدامات کاری ایمنی را طراحی نمایند تا خطرات فرا روی کارکنان در تولید و پاشش رنگ به حداقل برسد. این طرح باید شامل ملاحظات زیر باشد:
- بازبینی و کنترل
آ) میکس نمودن و ریختن
- انبار و جابجایی
پ) نگهداری و تمیزکاری
- فعالیتهای عمومی
- رویههای اورژانسی
- وسایل رفاهی و بهداشت
- میکس نمودن و ریختن
- موقع مخلوط نمودن رنگها و ریختن آنها، کارکنان باید مطمئن شوند که:
- میکس نمودن و ریختن
آ) تهویه خوب حفظ شود
ب) تمامی ظروف دارای اتصال ارت باشند
پ) وسایل محافظتی مناسب استفاده شود
ت) تمامی ریزشها و سرریزها باید فورا” تمیز شوند
- اگر مواد اسپری رنگ روی لباس و یا بدن ریخت، لباس آلوده را باید فورا” از تن خارج نمود و پوست را با آب و صابون شست. برای شستن پوست از حلالهای آلی استفاده نکنید.
- مایعات مازاد و یا استفاده نشده باید همواره به ظرف خودشان برگردانده شوند. اختلاط غیرضروری و یا تصادفی مایعات مختلف ممکن است خطرناک باشد و باید از آن اجتناب کرد.
- ظروف خالی ممکن است هنوز حاوی بخارات و یا حلالهای پسماندی باشند که تحت شرایط خاص منفجر شوند. بنابراین باید آنها را کاملا” تمیز و پس از استفاده به محلی ایمن منتقل نمود.
- انبار و جابجایی مواد خطرناک
- اقدامات مطمئن و ایمنکاری برای انبار و جابجایی مواد خطرناک در صنعت رنگ شامل موارد زیر است:
آ) درب ظروف باید بعد از هر بار استفاده تعویض شود.
ب) محل انبار مواد مشتعل باید خوب تهویه شود.
پ) ظروف باید دارای اتصال ارت مناسب باشند اگر حلالهای مشتعل شونده در آن قرار دارند تا الکتریسیته ساکن کنترل شود.
ت) مواد اسپری رنگ در محل اسپری باید تا حد امکان موجود نباشند یا خیلی کم باشند.
- مایعات اشتعالپذیر در ظروف خاص با برچسب مناسب ذخیره میشوند.
- ظروف مایعات اشتعالپذیر نباید در معرض نور مستقیم خورشید و یا نزدیک منابع گرما یا جرقه باشند.
- ظروف کوچک باید در داخل اتاقکهای محل انبار مواد اشتعالپذیر قرار گیرند.
- علائم هشدار دهنده باید در اتاقکها و بیرون محل انبار نصب شود تا توجه را به ماهیت خطرناک مواد ذخیره شده جلب نماید.
- مواد اسپری رنگ نباید در ظرف هایی به جز ظرف اصلی انبار یا نگهداری شوند. این امر در مورد ظرف مورد استفاده برای اسپری یا پوششکاری و یا ظرف مورد استفاده برای اختلاط رنگ برای استفاده فوری صدق نمیکند.
- تجهیزات و دستگاههای غیرضروری باید در اتاق اسپری و یا محل اسپری نگهداری شوند.
5-4- نگهداری و تمیزکاری
5-4-1- باید برای کشف زود هنگام عیوب اقدامات کنترلی و نقصهای آنها که حفاظت را به خطر میاندازد، برنامه نگهداری موجود باشد. موقع کار با مواد خطرناک، باید دقت لازم را به عمل آورد.
5-4-2- تمامی وسایل اسپری شامل شیلنگها و لولهها باید به صورت منظم بازرسی شوند تا در وضعیت خوبی باقی بمانند. هر گونه عیبی در دستگاهها و یا اقدامات کنترلی باید فورا” رفع شود.
5-4-3- تمامی دستگاههای اسپری باید به صورت منظم بر اساس دستورات سازنده تمیز و نگهداری شوند تا از ایمنی و بهداشت اپراتور محافظت شوند. فرآیند تمیزکاری باید در محیطی با تهویه خوب انجام شود.
5-4-4- تمامی نواحی مستعد تقویت پسماندها شامل دیوارها،کفها و سطوح کاری باید به صورت مکرر تمیز شود. غبارهای ناشی از سندبلاست و یا سمبادهکاری باید با استفاده از پارچههای مرطوب، جاروی تمیز کننده اقلام خیس و یا دیگر وسایل تمیز کننده اقلام خیس تمیز شود.
5-4-5- محل کارها باید تمیز و منظم باشند تا از خطرات دیگر اجتناب شود. از این گذشته، تأسیسات شستشو، اتاقهای تعویض و محل نوشیدن و خوردن باید دور از مواد خطرناک بوده و دارای تهویه مناسب باشد.
5-4-6- برای تسهیل برداشتن پسماندها از سطوح داخلی اتاقکهای اسپری، سطح باید با روکشهایی پوشانده شود که به خوبی با پسمانده از آن جدا گردد.
5-4-7- برای کاهش خطر احتراق لحظهای پسماندهای واکنشی مواد، اتاقکها و غیره باید تمیز شوند و قبل از تعویض باید فیلترهای خشک تعویض شوند.
5-5- فعالیت های عمومی پاشش رنگ
5-5-1- در زمان انجام فعالیتهای پاشش رنگ، شیئی که باید اسپری شود باید همیشه بین اپراتور و خروجی هوا باشد به گونهای که تأمین پیوسته هوای غیرآلوده از طریق منطقه تنفس اپراتور صورت گیرد و از روی جسم بگذرد. هر وقت ممکن شد، اسپری باید به سمت خروجی هوای اتاقک باشد.
5-5-2- برای جلوگیری از نشانه رفتن گان اسپری به سمت کارگران دیگر باید مراقب بود و باید اطمینان یافت که افراد دیگر در معرض آن قرار نگیرند.
5-5-3- تجهیزات غیر ضروری باید خارج از اتاقک باشند و باید موقع جابجایی و استفاده از وسایل تحت فشار دقت کافی داشت.
5-5-4- در مواردی که از اسپری هوای متراکم استفاده میشود، توازن صحیح هوا و مایع برای حداقل سازی تشکیل قطرات خیلی کوچک ضرورت دارد که معمولا” روی قطعه قرار نمیگیرند و باید برگشت قطرات از جریان را به حداقل رساند.
5-5-5- سیگار نکشید و از ایجاد شعله عریان و یا ابزارهای دیگری که احتمالا” سبب مشتعل شدن بخار مایعات قابل اشتعال میشوند خودداری کنید که این نواحی شامل اتاقک اسپری و تا شش متری هر محل اسپری میشود.
5-6- رویههای اورژانسی
5-6-1- حتی با وجودی که تمامی اقدامات کنترلی در حال اجرا باشد، باز هم ممکن است وضعیت اضطراری رخ دهد. به عنوان مثال، ممکن است با نشتی، سرریز و یا آزاد شدن کنترل نشده مواد خطرناک مواجه شویم که منجر به آتشسوزی شود. بنابراین طرح واکنش اضطراری باید ایجاد شود تا بتواند تمامی وضعیتهای اضطراری قابل پیشبینی را مدیریت نماید. این طرح باید شامل:
آ) واگذاری و تخصیص مسئولیتها و رویه ابلاغ باشد.
ب) دارای سیستم هشدار باشد.
پ) دارای رویههای پاسخ و واکنش اضطراری باشد.
- تمرینات اورژانسی برای تست آمادگی انجام شود.
5-6-2- در صورت نشتی و سرریز مواد خطرناک، باید رویههای اورژانسی داشت که شامل:
آ) دسترسی به PPE مناسب برای افراد موظف به شناسایی منبع آزاد شدن و انجام تعمیرات در صورت ایمن بودن شرایط
- خارج کردن تمامی افراد غیر مرتبط با وضعیت اضطراری از محل آلوده
پ) امحای ایمن مواد
برچسبها و MSDSتمامی مواد خطرناک در محل کار باید موقع برنامهریزی رویههای اضطراری مد نظر قرار گیرد.
5-6-3- در صورت بروز آتشسوزی، رویههای اضطراری باید تعیین شود که شامل موارد زیر است:
آ) هشدار دادن
ب) در صورت لزوم، درخواست از ادارات دولتی مانند پلیس و آتشنشانی برای کمک
پ) در وضعیت ایمن، اطفای حریق با وسایل آتشنشانی مناسب
ت) ارزیابی ایمنی محوطه
وسایل آتشنشانی شامل شیلنگها، کپسولها، پتوهای آتشنشانی و سیستمهای آب پاش میباشد. برای اطفای حریق مایعات اشتعالپذیر از کپسولهای حاوی پودر خشک یا کف استفاده کنید.
5-6-4- تمامی رویههای اضطراری باید مستند شود و نسخهای از آنها در محل کار باشد و به راحتی در دسترس تمامی افراد قرار گیرد.
5-6-5- دیگر وسایل اضطراری شامل چراغهای اضطراری و پشتیبانی برای خارج نمودن بخارات در صورت قطع برق، دوش و ایستگاه شستن چشم، کمکهای اولیه و مواد جاذب برای تمیز کردن سرریزهای کوچک شیمیایی اهمیت دارند.
5-6-6- تمامی تجهیزات اورژانسی باید به خوبی نگهداری و به صورت منظم چک شوند تا از عملکرد درست آنها مطمئن شوید. اقلام منقضی شده باید امحا و در مواقع لزوم تعویض و جایگزین شوند. محل تجهیزات اضطراری در محل کارها باید برای تمامی پرسنل شناخته شده باشد.
5-7- وسایل رفاهی و بهداشت
5-7-1- تأسیسات دستشویی و دیگر امکانات رفاهی باید تأمین شود. اتاقهای شستشو باید عاری از آلایندهها و دور از صدای ناشی از کار اسپری رنگ باشد.
5-7-2- اگر مواد خطرناک روی لباس و یا بدن پاشید، لباس آلوده باید فورا” خارج و پوست باید کاملا” با آب و تمیزکنندههای پایه آب تمیز شود.
5-7-3- اغلب حلالهای آلی از طریق پوست میتوانند جذب بدن شوند و بنابراین نباید برای تمیز کردن پوست استفاده شوند.
5-7-4- کارفرما باید مطمئن شود که آب و غذا و نوشیدنیها در اتاق اسپری نگهداری و یا آماده و یا مصرف نمیشوند و نیز این کار نباید در اتاق اختلاط و یا محل ریختن و یا هر ناحیهای انجام شود که احتمال آلودگی آن با مواد رنگی هست. کارگران رنگ کار باید PPE مورد استفاده را خارج و دستهای خود و صورت را قبل از خوردن و آشامیدن بشویند.
- اطلاعات، دستورالعملها و آموزش
- بازبینی و مرور
- بعد از ارزیابی ریسکها و اتخاذ اقدامات ایمنی مناسب در محیط کار، کارفرما باید مطمئن شود که کارکنان او خطراتی را که در سایتهای کار وجود دارد را میشناسند و درک میکنند و اقدامات کاری ایمن را انجام میدهند. برای رسیدن به این هدف کارکنان باید اطلاعات ایمنی، دستورالعملها و آموزش مناسب را در اختیار داشته باشند.
- اطلاعات، دستورات و آموزشها باید در مورد همه عوامل مربوط به رفتار انسان باشد. کارفرما باید بعد از مشورت با کارکنان خود طرحی مؤثر برای موارد زیر ارائه دهند:
- بازبینی و مرور
آ) پیشنهاد قوانین و دستورالعملهای ایمنی داخلی برای اسپری رنگ
ب) دسترسی به اطلاعات ایمنی ضروری برای کارکنان، مانند اموال و مواد شیمیایی خطرناک مورد استفاده در محل کار و اقدامات احتیاطی مربوطه
پ) ارائه خط مشی برای کارکنان
- اجرای اطلاعات، دستورات و آموزشهای کارکنان به روش:
- مشاهده، نظارت و بازرسی کارکنان در اجرای کارها
- فعالیتهای ترویجی برای افزایش اطلاعات ایمنی آنها
- اطلاعات و دستورات
- اطلاعات و دستورات باید به گونهای در اختیار کارکنان قرار گیرد که آنها موارد زیر را بشناسند و درک کنند:
- اطلاعات و دستورات
آ) اطلاعات در مورد مواد خطرناکی که کارکنان در معرض آن قرار میگیرند مانند ماهیت خطرات، ریسک برای سلامت، استانداردهای تماس با آن و مسیرهای ورود به بدن و غیره
- ماهیت و خطرات دستگاهها و سیستمهای کاری و دسترسی و استفاده از این اطلاعات
پ) برچسبزنی صحیح مواد خطرناک
- دسترسی به MSDSبرای مواد
- اقدامات مورد استفاده برای کنترل تماس با مواد خطرناک و ریسکهای دستگاهها
- رویههای اورژانسی
- رویههای کمکهای اولیه و گزارش حادثه
- بایگانی و نگهداری PPE توسط کارکنان
- اطلاعات و دستورات به طرق زیر میتواند در اختیار کارکنان قرار گیرد:
آ) صدور کتابچههای ایمنی، رویههای ماری و اورژانسی به عنوان ابزارهای اساسی و این اسناد باید در محلهای مناسب در محل کار نگهداری شوند و در دسترس همگان باشند.
ب) ابلاغیهها، پوسترها و فیلمهای مورد استفاده برای اطلاع رسانی ایمنی به کارکنان در مورد مدیریت مواد خطرناک و فرآیندهای اسپری رنگ
- آموزش کارکنان
- آموزش به کارکنان کمک میکند تا مهارتهای ضروری و دانش لازم برای استفاده از اقدامات ایمنی را فرابگیرند و از وسایل محافظ استفاده و پیرو دستورات اضطراری باشند. آموزش باید کارکنان را مطمئن سازد تا در تصمیمگیریهای مربوط به ایمنی و بهداشت محل کار مشارکت نمایند.
- کارکنان باید اطمینان یابند که تمامی افراد درگیر به صورت مستقیم و غیر مستقیم در فرآیندهای اسپری رنگ قبل از آغاز کار به خوبی آموزش دیدهاند.
- آموزش شامل موارد زیر است:
آ) دلایل و ماهیت اقدامات کنترلی مورد استفاده یا برنامهریزی شده
- اقدامات کاری و رویههایی که باید در استفاده، مدیریت، انبار، انتقال، تمیزکاری و امحای مواد خطرناک مدنظر باشد.
پ) اقدامات کاری ایمن در بهره برداری از وسایل اسپری رنگ و انجام فرآیندهای اسپری رنگ
- گزارش خطاها و رخدادها
- انتخاب، استفاده و نگهداری وسایل حفاظت فردی
- استفاده از تجهیزات و وسایل اضطراری
- آموزش باید فرآیندی جاری باشد به گونهای که کارکنان در مورد توسعه و دستاوردهای جدید بیاموزند و مهارتها و دانش آنها بهبود یابد. آموزشهای نوین باید به ویژه در اختیار کارکنان برگشته از مرخصی طولانی و یا برگشت به کار بعد از یک دوره طولانی غیبت و تغییرات در محل کار و از رده خارج شدن و قدمی شدن اطلاعات و آموزشهای قبلی، قرار گیرد.
- آموزش باید بازبینی شود تا مطمئن شویم که کارکنان مهارتهای بروز و دانش نوین مورد نیاز را یاد میگیرند. کارفرماها نیز باید اطمینان یابند که کارکنان آنها بعد از آموزش، آموختههای خود را درک میکنند.
- کارکنان باید آموزشها را ثبت نمایند که شامل:
آ) اسامی کارکنان آموزش دیده و تاریخهای حضور آنها
ب) توضیحات محتوی دوره
پ) اسامی و مدارک افراد آموزش دهنده است.
- موضوعات خاص
- حلالهای آلی
- به استثنای آب، تمامی حلالها ( تینر و رقیق کننده) مورد استفاده در تولید و اسپری رنگ ترکیبات آلی فرار است. یکی از رایجترین انواع این ترکیبات تولوئن، زایلن، متیل اتیل کتون، استون، بنزن و مشتقات اتیلن گلیکول، تارپنتین و نفت سفید است.
- حلالهای آلی ممکن است از طریق استنشاق به شکل بخارات و یا رطوبت وارد بدن شود. آنها از راه پوست و جذب آن از طریق تماس مستقیم با دستها و بازوی کارگر وارد بدن شوند.
- تماس کوتاه مدت با حلالهای آلی میتواند سبب علائم زیادی مانند حساسیت چشمها، گلو، ششها و معده شود. سردرد، تهوع و احساس مستی و احساس تغییر و عوض شدن ممکن است رخ دهد. اگر تماس خیلی شدید باشد، بی هوشی و حتی مرگ هم ممکن است رخ دهد. تماس طولانی ممکن است روی کار خونسازی بدن، ششها، کلیهها و سیستم عصبی اثر بگذارد. تماس مکرر با پوست نیز ممکن است منجر به از دست رفتن چربی پوست و التهابات پوستی حاد شود.
- PPE مناسب مانند دستکشها، پوتینها، استر و پیشبند باید برای کارکنانی فراهم شود که با حلالها سروکار دارند. MSDS هر حلال مورد استفاده در محل کار نیز باید از تأمین کنندهها اخذ شود تا ایمنی کامل و اطلاعات بهداشتی داشته باشیم که شامل انتخاب PPE مناسب میشود.
- موقعی که کنترلهای مهندسی فورا” عملی نباشند، حفاظت تنفسی مناسب میتواند به صورت موقت اتخاذ شود. استفاده از ماسکهای کامل و نیم ماسک با محیط جاذب مناسب برای بخارات آلی باید در نظر قرار گیرد.
- حلالهای آلی هرگز نباید برای تمیز کردن دست استفاده شود. قسمتهای پوست در تماس با حلالها باید فورا” با آب و صابون شسته شوند.
- سرب
- تولید و اسپری رنگ با پایه سرب ممکن است سبب تماس شدید با سرب شود که میتواند از طریق استنشاق، هضم و جذب پوستی وارد بدن شود.
- کارگرانی که از وسایل اسپری هوای متراکم عادی استفاده میکنند در معرض اسپری اضافی و برگشت اسپری رنگ با پایه سرب قرار میگیرند که سبب افزایش خطرات استنشاق شود.
- اثرات بهداشتی حاد سرب شامل موارد زیر است:
- حلالهای آلی
آ) کم خونی
- حساسیت پوستی
پ) تهوع و درد معده
ت) حساسیت چشمی
- حساسیت غشای مخاطی
- اختلال در سیستم عصبی
- اثرات بهداشتی حاد سرب شامل موارد زیر است:
آ) اختلالات تناسلی
ب) کم خونی
پ) آسیب دیدن سیستم عصبی و کلیهها
- حد تماس شغلی یا میانگین زمانی وزنی سرب و ترکیب سرب غیر آلی 05 mg/m3 است.کارفرماها باید اقدامات لازم را برای اطمینان از این مهم انجام دهند که میزان سرب در هوای منطقه تنفس هر کارگر کمتر از این سطح است.
- اقدامات زیر باید سبب کاهش تماس کارگران و یا ممانعت از تماس آنها با سرب در زمان تولید و پاشش رنگ و یا فرآیندهای پوششکاری شود:
آ) استعمال رنگ های بدون سرب
ب) تعویض کرمات سرب با روی
پ) استعمال رنگ با پایه سرب با برس و یا روشهای غلتکی به جای روشهای اسپری نمودن
ت) استفاده از تهویه خروجی موضعی مناسب با فیلتراسیون صحیح
- PPE مناسب باید برای کارکنان درگیر در اسپریکاری و فرایندهای پوششکاری مربوطه فراهم شود.
- کارکنان باید دارای اطلاعات مناسب و آموزش درباره خطرات مسمومیت سربی و اقدامات پیشگیرانه در این رابطه باشند. آنها باید از وسایل و تجهیزات ارائه شده استفاده نمایند و با کارفرمای خود همکاری کنند تا پخش آلودگی سربی محدود شود.
- رنگهای دو جزئی
7-3-1- رنگهای دو جزئی شامل انواع پلی یورتان، اپوکسی و سیستمهای اکریلیک دارای یک پایه یا بخش A و یک سختکننده یا کاتالیست یا بخش B هستند. به عنوان مثال پلی یورتان ساختار پلیمری پیچیده است که با واکنش دی ایزوسیانات با پلی ال به دست میآید.
7-3-2- رنگهای دو جزئی و یا لاکهای حاوی دی ایزوسیانات اغلب به شکل اسپری استفاده میشوند تا پوشش سخت، با دوام و راحت پاک شوندهای ایجاد شود که در آن دی ایزوسیانات به رزینهای مایع و رنگدانهها اضافه میشود تا یک فیلم پلی یورتان ایجاد شود. بخارات و اسپریهای حاوی ایزوسیانات به شدت برای چشم ها و دستگاه تنفسی مضر هستند و میتوانند سبب تنگی نفس شغلی و کاری شوند.
7-3-3- لباسهای کاملا” محافظ مانند روپوشهای یکبار مصرف باید استفاده شوند. دستکشهای نیتریل نیز باید استفاده شود تا از جذب پوستی جلوگیری گردد. تمامی بخشهای باقیمانده پوست باید با یک کرم محافظ پوشانده شود زیرا این رنگها به خوبی میچسبند. برای استفاده از پلی یورتان دو جزئی از ماسک تمام صورت استفاده شود. برای اپوکسی و یا اکریلیک اگر ماسک ایرلاین نبود از ماسک تمام صورت دارای کارتریج بخار آلی با پیش فیلتر استفاده شود اما باید مدت استفاده از آن کم باشد.
7-3-4- سیستمهای رنگ دو جزئی تنها باید توسط افراد ذیصلاح و ماهر و آموزش دیده استفاده شوند.
7-3-5- رنگهای دو جزئی باید در داخل یک اتاقک اسپری شوند در غیر این صورت باید آنها را با قلم مو یا غلتک زد.
- اسپری نمودن در فضاهای بسته
- روش اسپری اغلب برای زدن پوشش در فضاهای بسته استفاده میشود مثلا” در داخل مخازن و یا در اتاقهای بسته و یا در فضاهای بسته انجام میشود. در فضای بسته بدون تهویه، غلظت بخارات مضر در عرض چند ثانیه بعد از آغاز کار زیاد میشود و فضای قابل اشتعالی در عرض چند دقیقه ایجاد میشود.
- اسپری نمودن در فضای بسته صنعتی باید بر اساس قوانین فضاهای بسته در بخشهای صنعتی و کارخانهها انجام شود. آیین نامه عملی: ایمنی و بهداشت کار در فضاهای بسته راهنمای عملی و اطلاعات فنی را برای پیمانکاران و دیگر شاغلین در بخشهای صنعتی ارائه میدهد تا از ایمنی و بهداشت تمامی افرادی که وارد فضاهای بسته میشوند و یا در آن کار میکنند مطمئن شویم.
- کارکنان درگیر در اسپری رنگ در محیطهای بسته باید آموزشهای ایمنی خاص را دریافت و خطرات را بشناسند. مجوز ورود مکتوب رسمی و یا مجوز کار برای ورود به محوطههای بسته الزامی است.
- تهویه مکانیکی باید فراهم شود تا مطمئن شویم که غلظت مواد خطرناک در تمامی بخشهای فضای محبوس در سطح ایمن است. با تجمع بخارات اسپری در سطح کف، باید آن را بیرون کشید. نقطه تخلیه باید در فاصله ایمن از هر ساختمان، محل کار و یا منبع جرقهای باشد. وقتی تغییراتی در شرایط اسپری رخ دهد مثلا” وقتی تعداد اسپری کنندهها افزایش یابد و یا مواد روکشدار فرار بیشتری استفاده شود، ارزیابی مجدد کارایی تهویه ضرورت دارد.
- پایش و کنترل جوی پیوسته برای آشکارسازی افزایش سطح بخار بیش از حد تعیین شده در فرآیند اسپری یک ضرورت است. وسایل عادی مورد استفاده آشکارساز گاز و یا انفجارسنج هستند که ترجیحا” باید دارای هشداردهنده باشند.
- گذاشتن منابع جرقه داخل یک فضای بسته اکیدا” ممنوع است و روشنایی و لامپها باید دارای حفاظ باشند. وسایل بدون حفاظ مورد استفاده مانند موتور فنها، کمپرسور، سوئیچ ها و هشداردهنده ها باید در ناحیه ایمنی بیرون از فضای محبوس باشند که در آن در معرض بخارات قابل اشتعال قرار ندارند.
- تهویه یک فضای محبوس بسیار اهمیت دارد تا وقتی که پوشش خشک شود و خطر فضای قابل اشتعال موجود نباشد. هر گونه تجمع بخارات قابل اشتعال در داخل فضای بسته میتواند در اثر گرمکاری بیرونی محترق شود.
- خطرات جرقه در اسپری الکترواستاتیک
- در یک سیستم اسپری الکترواستاتیک، قطرات ریز تفنگ اسپری به صورت الکتریکی جذب قطعه میشوند. این بخش میتواند میزان برگشت و اسپری اضافی را کم کند.
- جرقه بخار حلال توسط تخلیه الکتریکی سبب ایجاد خطرات خاصی برای اسپری الکترواستاتیک میشود. به طور کلی، ممکن است در اثر تخلیه الکتریکی مستقیم از تفنگ به قطعه و یا با تخلیه برق از یک قطعه بدون ارت رخ دهد. این کار سبب ایجاد خطر جرقه الکتریکی در نازل اسپری و در سطح خیس قطعه میشود.
- با توجه به خطرات جرقه، باید اقدامات احتیاطی زیر را انجام داد:
آ) وسایل جرقه باید تنها توسط افراد دارای صلاحیت استفاده شوند.
- اسپری الکترواستاتیکی باید در اتاق اسپری و در محیط اسپری خاص این کار انجام شوند. تمامی منابع جرقه بخارات حلال و پسماندهای آن باید از مجاورت قطعه کار دور شوند.
پ) اتاقکها و حصارهای مشابه باید مقاوم به حریق و دارای تهویه مناسب باشند.
ت) تنها تفنگ اسپری و سیمهای متصل به آن باید در اتاق اسپری و یا محل اسپری باشند. تمامی وسایل الکتریکی مربوطه مثلا” پاورپک، کمپرسور موتور دار و اتصالات اصلی باید در بیرون محل باشند و یا در محیطی جدا در سازههای مقاوم به آتش سوزی محصور گردند مگر این که دستگاهها دارای تأییدیه استفاده در منطقه خطر باشند.
ث) تمامی سطوح فلزی و تجهیزات در شعاع 3 متری از سر باردار تفنگ اسپری باید اتصال بدنه داشته باشند تا از تجمع بارهای استاتیکی منجر به جرقه جلوگیری شود.
- هر فردی در اتاق اسپری و یا در محل اسپری که ممکن است در حین کار بار دریافت نماید نباید اقلام فلزی تن کند و باید لباس مناسب برای جلوگیری از ایجاد و تجمع بار الکتریکی داشته باشد.
- کارگران باید از پای افزار رسانا و ضد الکتریسیته ساکن استفاده نمایند تا مانع تجمع بار الکترواستاتیک در بدنه شوند.
- هنگام انجام کار اسپری نمودن، قوطی رنگ و یا حلالهای پاک کننده نباید در اتاق اسپری و یا محل اسپری باشند.
- حلال تمیز کننده برای نازل اسپری باید دارای نقطه اشتعالی باشد که از 23 درجه کمتر است و از دمای محیط بالاتر است. تنها ظروف حلال فلزی دارای اتصال ارت باید استفاده شود و نازل نباید در صورت برق داشتن با ولتاژ بالا تمیز شود.
منابع
- Code of Practice on Safety Management, 2002
- Code of Practice on Control of Air Impurities (Chemical Substances) in
the Workplace, 2002
- Chemical Safety in the Workplace: Guidance Notes on Risk
Assessment and Fundamentals of Establishing Safety Measures, 2001
- Chemical Safety in the Workplace: Guidance Notes on Personal
Protective Equipment for Use and Handling of Chemicals, 2002
- ISO 11014-1 “Safety Data Sheet for Chemical Products”, 1994,
Geneva, Switzerland
- Five Steps to Risk Assessment, 1999, HSE, UK
- The Spraying of Flammable Liquids, 1998, HSG178, HSE, UK
- Spraying of Highly Flammable Liquids, 1987, Guidance Note EH9,
HSE, UK
- National Guidance Material for Paint Spraying, 1999, NOHSC,
Australia
- Code of Practice: Spray Painting, 2000, WorkSafe Western Australia
Commission, Australia